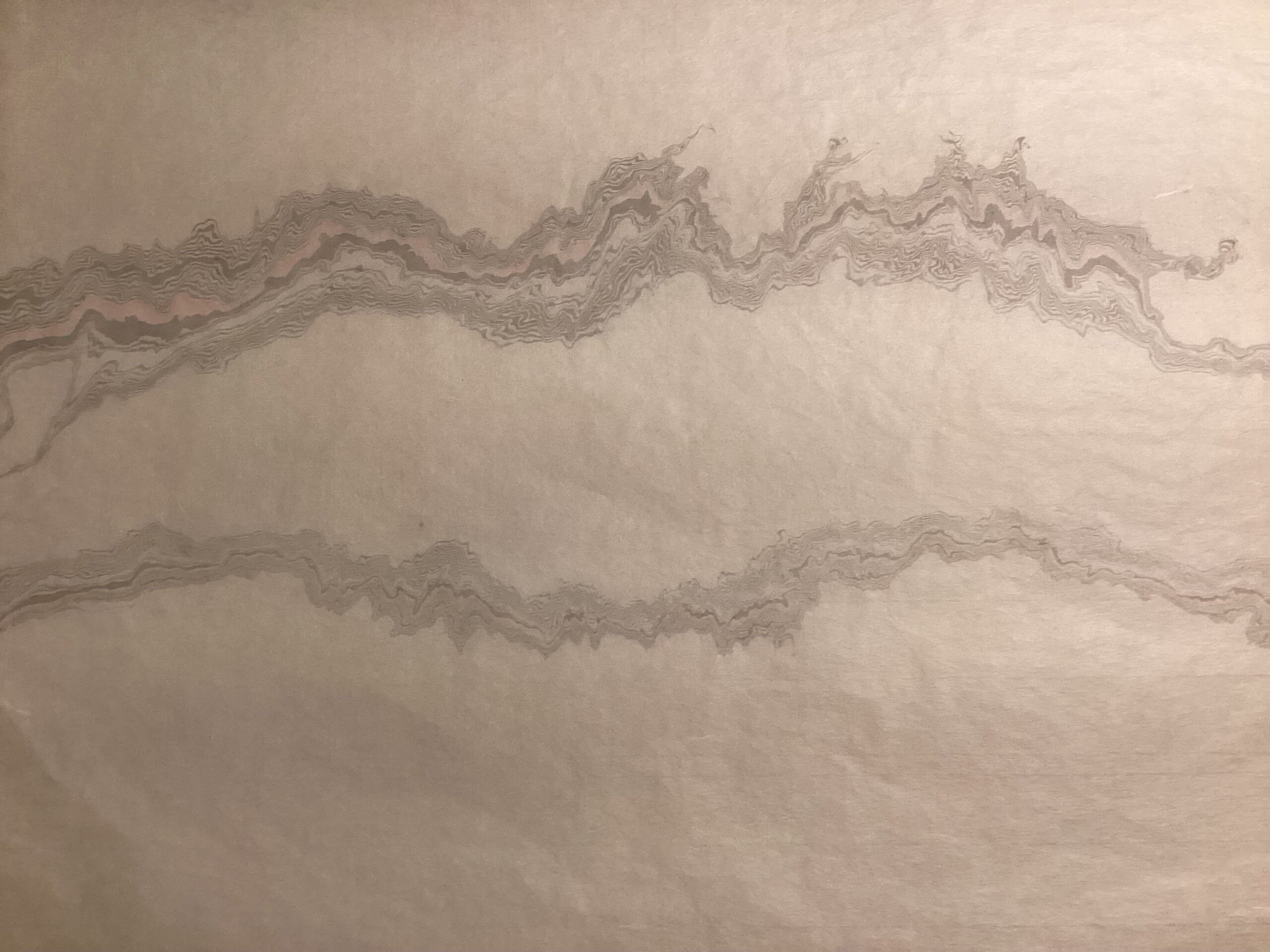
For most of its history, suminagashi has been made using black/sumi ink. We have no information about how the ink was prepared. A good assumption might be that the ink was made by grinding an ink stick on an ink stone (suzuri) as is typically done for calligraphy. However, I have not found that ink prepared this way works very well, particularly when trying to further manipulate the pattern after the initial rings of ink are made. For a comparison of different inks see the Ink comparison page. Since I made watercolor paint for western style paper marbling for years, I have used that knowledge as a basis for making ink for suminagashi.
The primary ingredients of a paint are the pigment, a binder, and a solvent. With water-based paints, the binder is usually a glue of some kind. Traditionally, for watercolor paint, it is gum arabic. However, many other binders have been used over the centuries. In Japan, hide glue has been used as the binder both for making sumi ink sticks and for painting (Nihonga). The binder serves two purposes: it enables uniform distribution of the pigment throughout the paint, so a smooth film can be achieved (otherwise the pigment particles would clump), and it serves as a glue, binding the pigment to the surface, in this case, of the paper.
The concentration of hide glue in the binder is very important for proper ink flow in the finished ink. In my experiments in making ink I observed that too strong hide glue binder resulted in the ink lines fracturing when compressed. I found that binder concentration of 2 grams per 100 ml water was optimal for the pigments I was working with.
To make the paint/ink, place pigment in a mortar (the amount depends upon the size of the mortar) and add enough binder to make a paste, using the pestle to blend and smooth out the paste (for larger volumes of ink you can used a muller and slab, but since suminagashi uses such small amounts of ink I found this unnecessary). Some pigments, lamp black in particular, do not wet easily, so this can take some time and careful mixing (always wear a particle mask when working with pigments). Once the pigment is universally moistened, about 5 minutes of additional grinding with the pestle will generally suffice to make the paint smooth, uniform and able to be used. Some pigments will not work well for suminagashi ink. Usually, it is a matter of trial and error to find ones that work satisfactorily. The use of blue and red introduced during the Edo period was likely adopted from the woodblock printing trade, ukiyo-e: red most likely from safflower and blue from either indigo or dayflower. For the three classic colors, I use lamp black for the black, synthetic indigo for the blue (genuine indigo is preferable but more granular and much harder to grind) and irgazine red for the red/pink. These work reliably well.
The table below lists the ingredients, purpose and proportions to make 250 mls of binder.
To make the binder, warm distilled water in a jar in a double boiler (water temperature not to exceed 140 degrees Fahrenheit) and add the hide glue, stir and allow the glue to dissolve. Let the mixture cool, then add the preservatives and the vinegar. The binder and paint should be refrigerated for storage, although the preservatives will generally prevent spoiling for many months.
Ingredient | Amount | Function |
Hide glue | 5 grams | binder |
Sodium benzoate | 0.5 grams | preservative |
Potassium sorbate | 0.5 grams | preservative |
White vinegar | 8 milliliters | acidifier |
Distilled water | 250 milliliters | solvent |